In the demanding world of construction, infrastructure, and industrial development, one material continues to underpin our progress: steel. Its strength, versatility, and affordability have made it indispensable across Australia’s toughest sectors—from mining and agriculture to marine and manufacturing. But despite its many advantages, steel has a vulnerability that can’t be ignored: corrosion.
Whether it’s salt-laden winds on the coast, ammonia-heavy air in fertiliser plants, or chemical exposure in industrial zones, steel left unprotected will deteriorate fast. In these environments, traditional coatings often fall short. That’s why advanced coating technology isn’t an industry novelty, it’s a necessity.
What Makes Environments “Harsh” for Steel?
Australia’s environment is beautiful, but brutal on infrastructure. Many of our key industries operate in highly corrosive conditions:
Marine areas face high levels of salt spray, which accelerates rust and structural degradation.
Mining regions contain abrasive dust and chemicals that eat away at exposed surfaces.
Agricultural zones often involve fertilisers and high humidity that contribute to rapid corrosion.
Feedlots are at great risk of corrosion due to the use of ammonia.
Each of these factors alone can compromise conventional galvanised steel where its coating is insufficient for long-term performance.
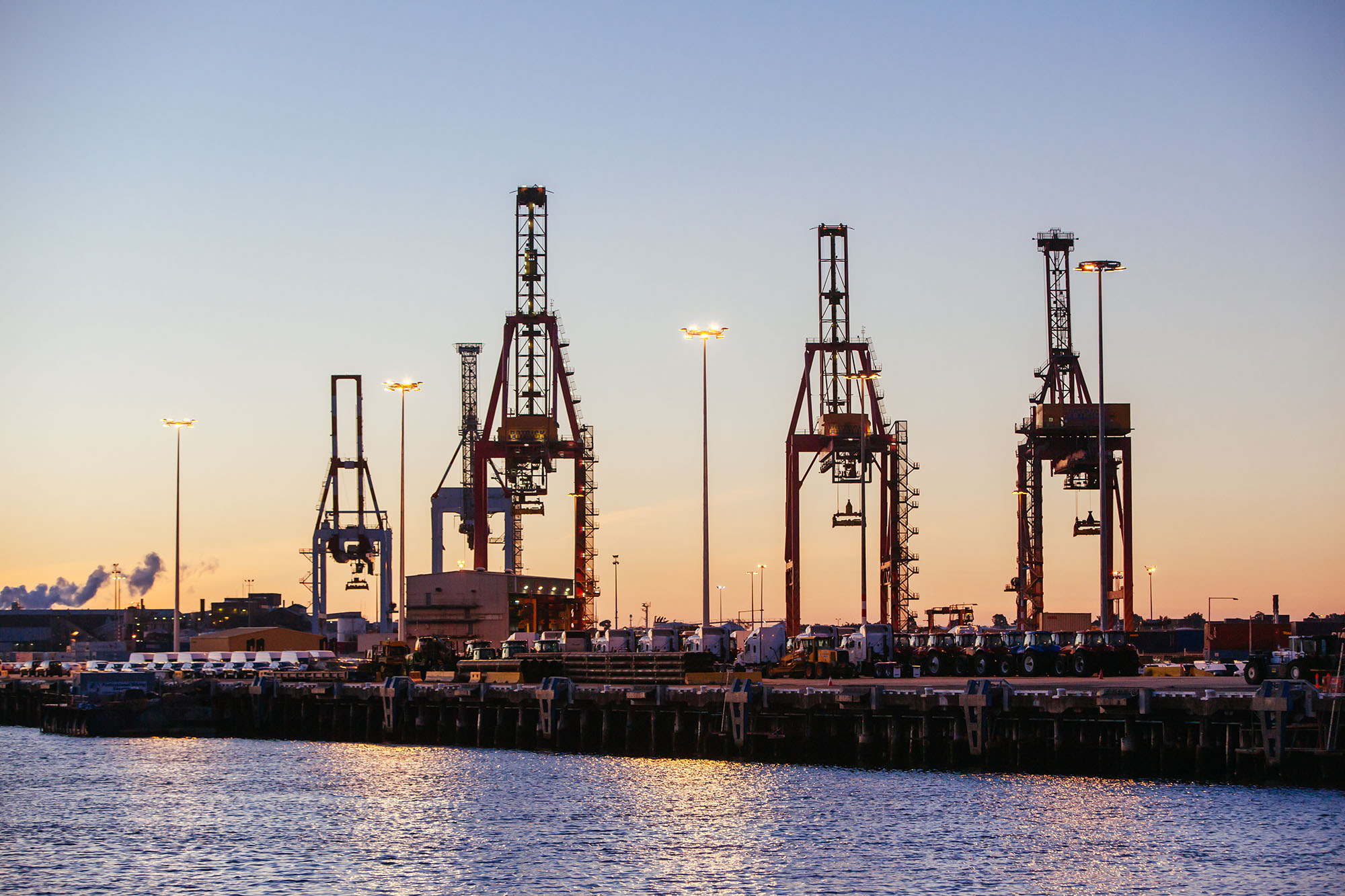
Why Is Advanced Coating Necessary?
In conditions like these, advance coating is not optional—it’s the frontline defence against environmental wear. Here’s why it’s crucial:
Corrosion Resistance: An advanced coating prevents oxidation and material degradation, maintaining structural integrity even in highly corrosive environments.
Extended Lifespan: Coated steel with the right blend of protective materials can last three to five times longer than standard galvanised products.
Reduced Maintenance: With better durability comes less need for repair, repainting, or component replacement—saving money and downtime.
Smarter Investment: For asset owners, procurement personnel and engineers, investing in long-lasting materials means better lifecycle value—not just a lower upfront cost.
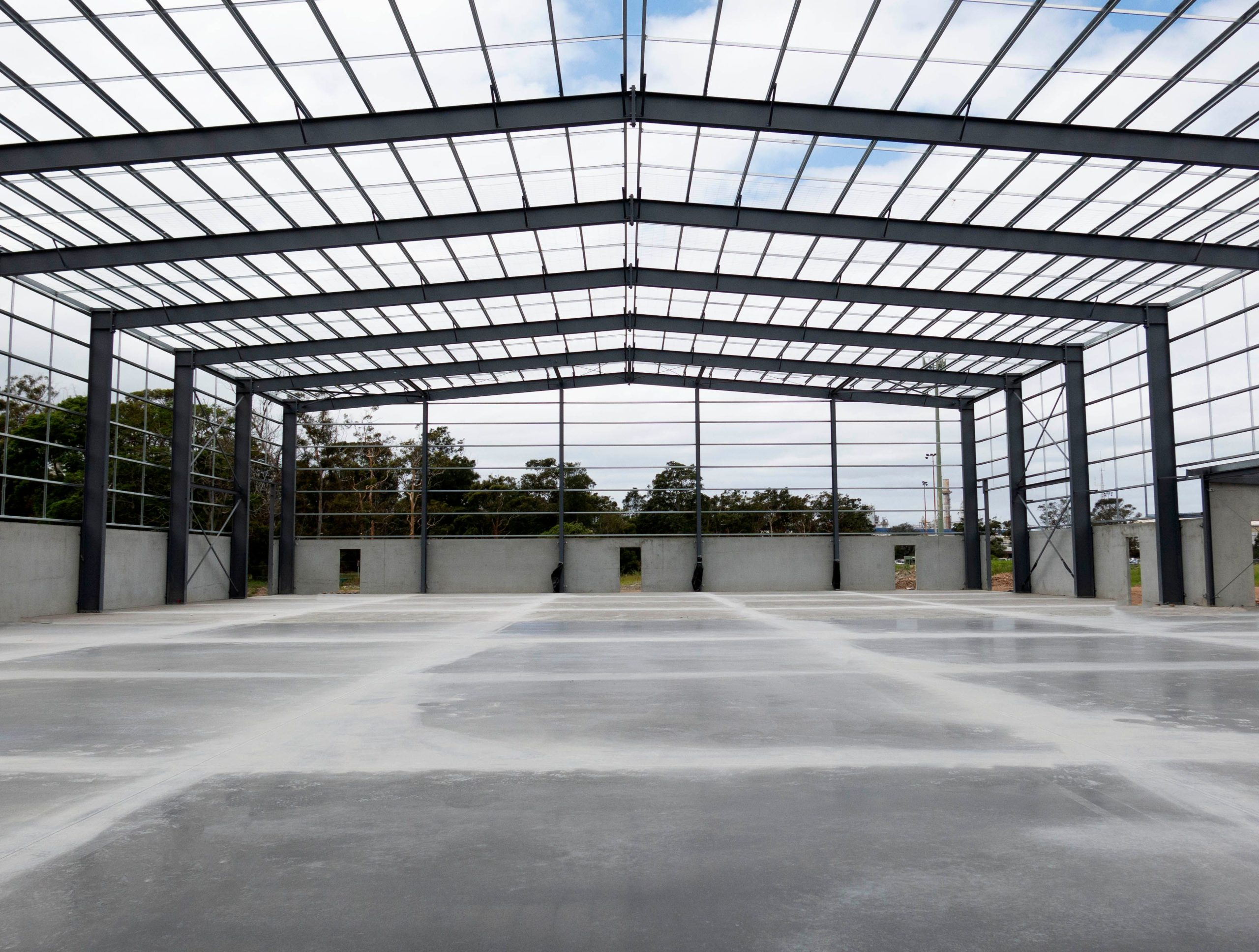
Modern Steel Solutions for Modern Challenges
Today’s smart steel solutions are about more than the metal itself, they’re about the protective technologies that make steel perform better for longer. Steel coating technology has become a vital part of value-added supply, particularly in a country like Australia where climate and industry collide.
Meeting evolving infrastructure standards requires smarter thinking. Advanced coatings like Millform’s MAGNA-SHIELD PRO™ (MSP) demonstrate how forward-thinking materials can meet the demands of durability, sustainability, and performance—without major cost increases.
How Advance Coating Works
So what makes advanced coating different from traditional galvanising?
Let’s take MAGNA-SHIELD PRO™ (MSP) as a benchmark. It uses a unique ZM350 coating, combining zinc, 5% aluminium, and 3% magnesium. This trio provides exceptional corrosion resistance, particularly in salt-heavy and chemical-prone environments.
MSP features:
- Multi-layer protection that resists corrosion even in high-salinity zones
- Scratch resistance that holds up in real-world construction conditions
- Self-healing properties on cut edges, preserving protection after fabrication
- No need for post-galvanising, streamlining production and reducing lead times
Independent testing has shown MSP outperforms traditional hot-dip galvanising—offering 3-5x longer performance in coastal and industrial environments.
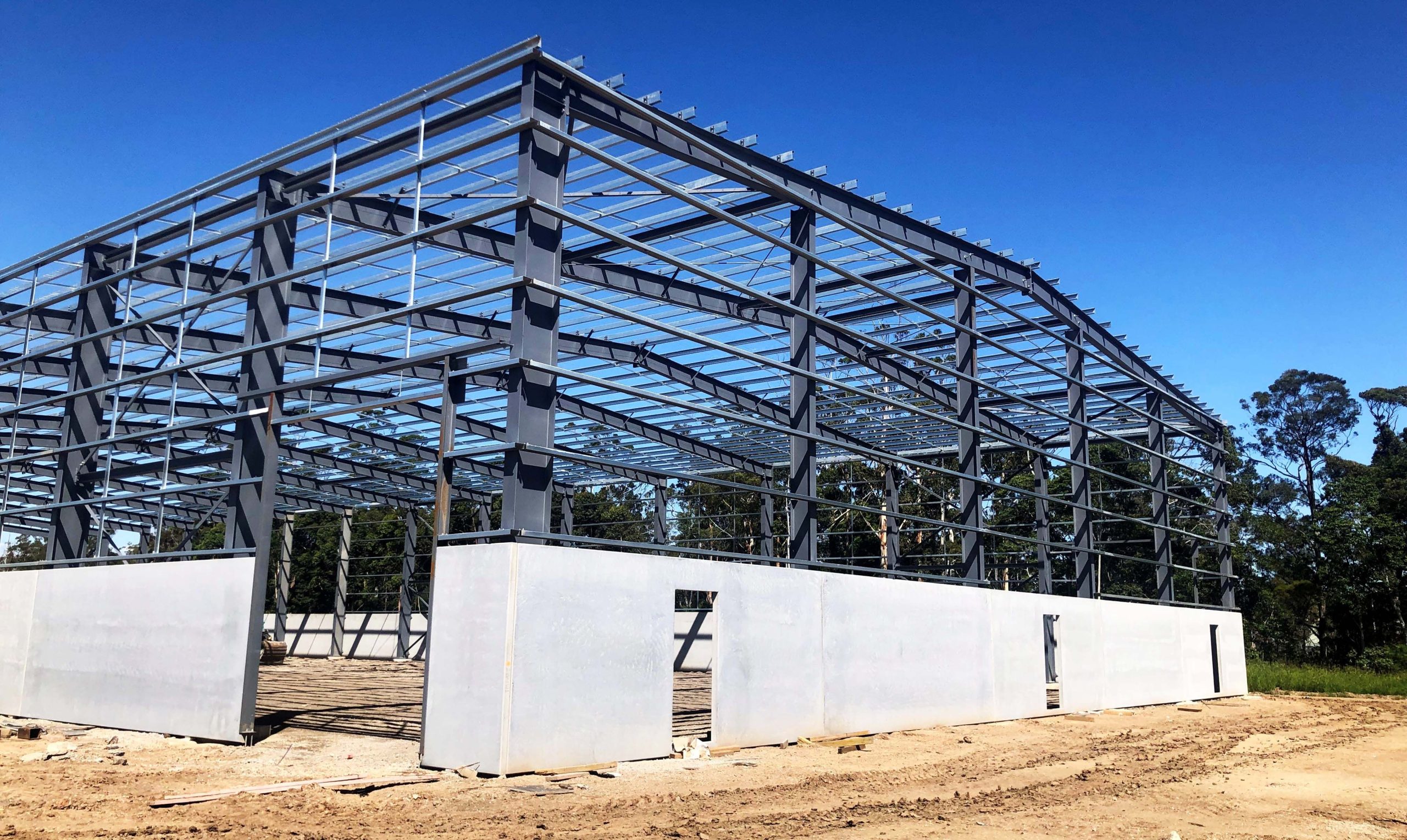
Spotlight on Steel Production in Australia
Demand for steel products in Australia is on the rise, powering everything from urban development to energy and transport infrastructure. With this growth comes a responsibility to ensure the materials we use are built to last.
Industry bodies and government regulators are increasingly prioritising durability, efficiency, and environmental responsibility. That’s where solutions like MSP make sense: they align with long-term investment strategies while offering unmatched protection.
By selecting advanced coated steel at the outset of a project, builders and engineers are making a smart bet on future performance, safety, and compliance. Here’s a recent story of how MSP helped Spanlift Australia achieve just that:
Case Study: Cowell Fertiliser Distribution Facility, SA
A recent project on South Australia’s Eyre Peninsula demonstrates the real-world value of MSP. In Cowell, just 2km from the ocean, Spanlift Australia developed a 10,000 sqm fertiliser distribution facility.
Primary Challenge: The combination of salt air and fertiliser dust created one of the most corrosive environments imaginable. Spanlift needed a solution that could handle both coastal salt spray and the naturally corrosive nature of fertilisers.
Why MSP? After evaluating multiple options, Spanlift chose MAGNA-SHIELD PRO™ (MSP) for its unmatched performance in similar environments.
Key Advantages:
- The ZM350 coating delivered at least three times the lifespan of standard galvanised steel.
- Independent testing confirmed superior salt spray resistance.
- The uniform finish enhanced both aesthetic and structural quality.
Result: Early feedback has been highly positive. Spanlift’s construction team praised the ease of installation, and the client noted the improved durability and finish. With MSP in place, the facility is now positioned for long-term structural integrity and lower maintenance costs.
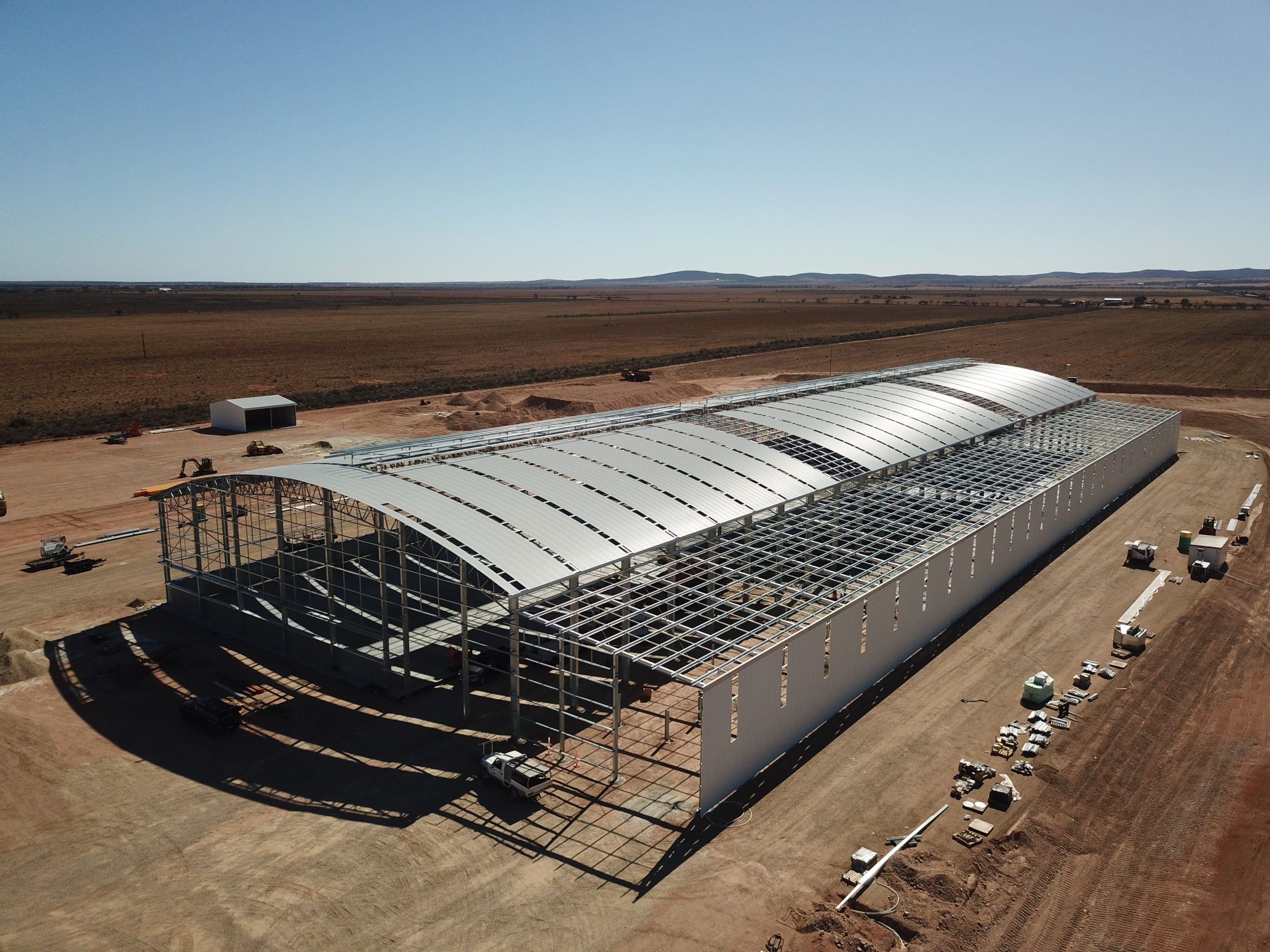
Millform’s MAGNA-SHIELD PRO™ (MSP): Future-Ready Protection
Built for tomorrow, MAGNA-SHIELD PRO™ (MSP) redefines what steel can achieve in harsh Australian conditions.
Key features include:
- 3–5x the lifespan of traditional galvanised steel
- Superior corrosion protection for coastal, marine, chemical, and agricultural sites
- Easy compatibility with powder coating
- Lower long-term costs with reduced maintenance needs
- Faster lead times, thanks to no post-galvanising
Whether you’re working on an industrial plant in WA, a wharf in QLD, a fertiliser facility in regional SA, or an agricultural feedlot in VIC or NSW—MSP offers a smarter, stronger solution.
Millform’s MSP isn’t just a product. It’s a statement: that the future of steel in Australia depends on performance, reliability, and innovation.
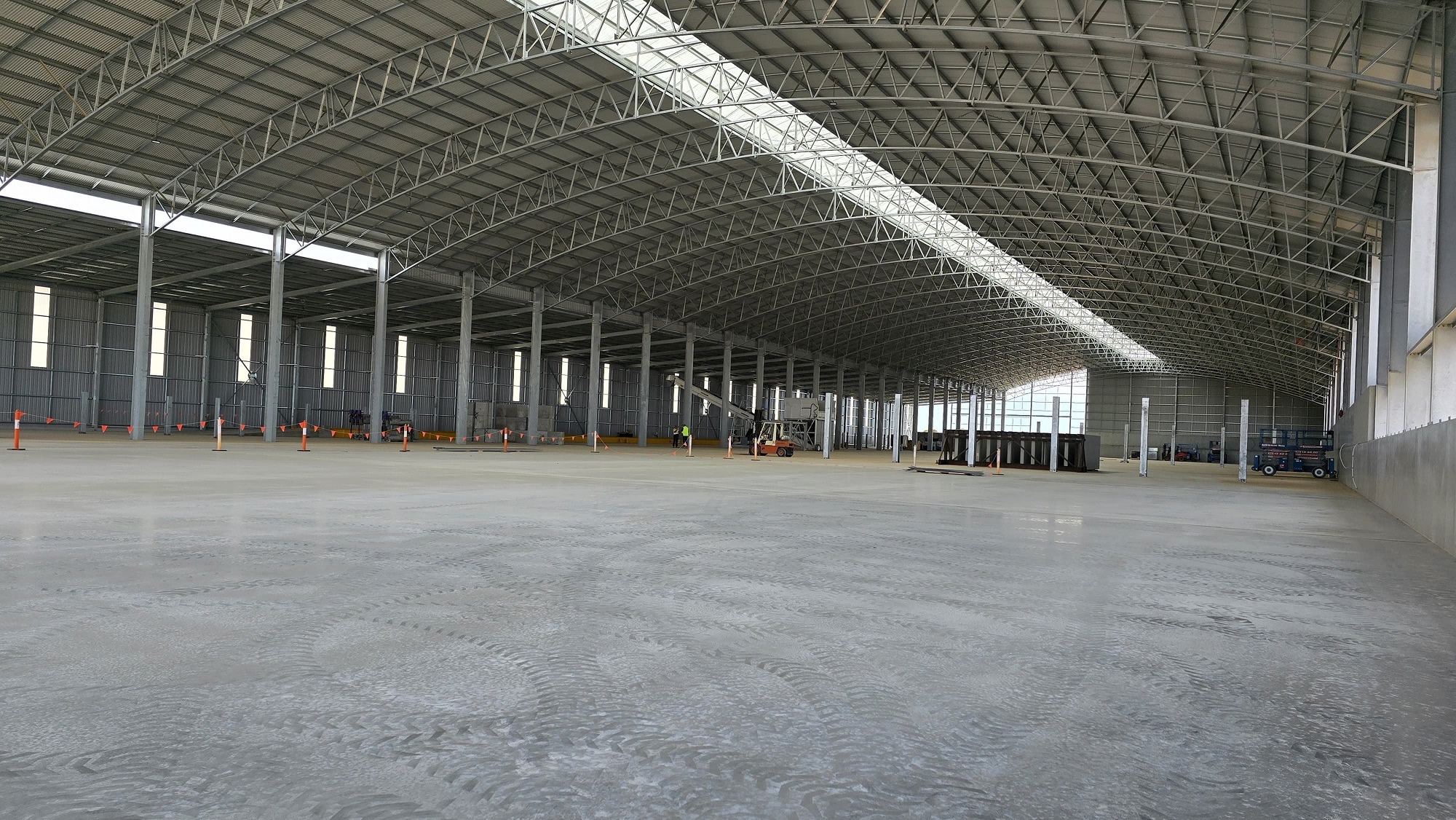
Conclusion: Protect Now or Pay Later
Corrosion doesn’t wait. Whether in harsh Australian conditions, or highly corrosive facilities, it doesn’t take long for untreated or traditional galvanised steel to fail. That’s why advance coating is essential, not just for meeting today’s challenges, but for securing tomorrow’s infrastructure.
MAGNA-SHIELD PRO™ (MSP) sets a new benchmark in industrial protection, offering the harsh environment durability and long-lasting steel performance that engineers, construction contractors, and procurement teams can trust.
From owners of steel building structures to government facility managers, the message is clear: protect your assets from day one, or risk greater costs later.
Protect your steel investments before corrosion becomes a costly problem. Learn more about MAGNA-SHIELD PRO™ (MSP) from Millform—Australia’s trusted leader in durable steel coating solutions. Contact us today for expert guidance.